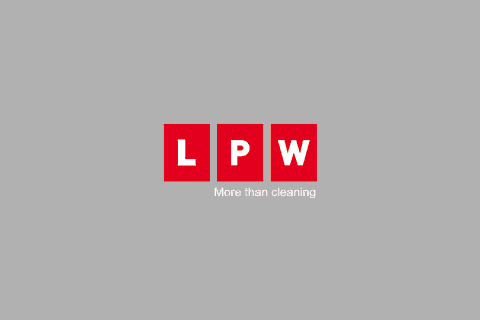
Feinreinigung bedeutet, ein gleichbleibendes hochwertiges Reinigungsergebnis im Dauerbetrieb nach vorgegebenen Restschmutzmengen und gemeinsam festgelegtem Verfahren zur Restschmutzbestimmung zu erzielen.
In Verbindung mit optimierten Behälter- und Rohrleitungsausführungen, können Rückverschmutzungen durch filmische oder partikuläre Anhaftungen im Medienkreislauf vermieden werden. Zur Fein-/Feinstreinigung eignen sich im Besonderen ergänzende prozesssichere waschmechanische Verfahren wie die Zyklische Nukleation (CNp), die Ultra-/Megaschallreinigung sowie das Injektions-/Druckfluten, da mit diesen Verfahren höchste Reinheitsgrade erzielt werden können.
Besondere Bedeutung haben die Aspekte der optimalen Spülqualität sowie die Vermeidung Re-/Crosskontaminationen sowie von Medienverschleppung.
Die Abgrenzung nach der Art der unerwünschten Verunreinigung, der geforderten Zielgröße allein reicht nicht aus. Die Auslegung einer Reinigungsanlage auf die Feinstreinigungsanforderungen der Automobilindustrie, etwa bei Einspritzsystemen, erfordert dieselbe Sorgfalt und denselben Aufwand, wie die Planung und Erstellung einer Reinigungsanlage für die Medizintechnik, der Halbleiterproduktion oder der optischen Industrie. In puncto Umwelt- und Rahmenbedingungen in Relation zu den notwendigen Reinheitsanforderungen ist eine unterschiedliche Herangehensweise gefragt, da physikalische und chemische Grenzen von Komponenten, Fluiden, Gasen und Zusatzstoffen ggf. anders Einfluss nehmen.
Basis aller Feinstreinigungsthemen ist jedoch, dass sie ohne direkte Zusammenarbeit zwischen dem Anlagenbauer und dem Kunden wenig Aussicht auf Erfolg haben. Der Aspekt Technische Sauberkeit ist bei all diesen Projekten eine Aufgabenstellung an die gesamte Prozesskette.