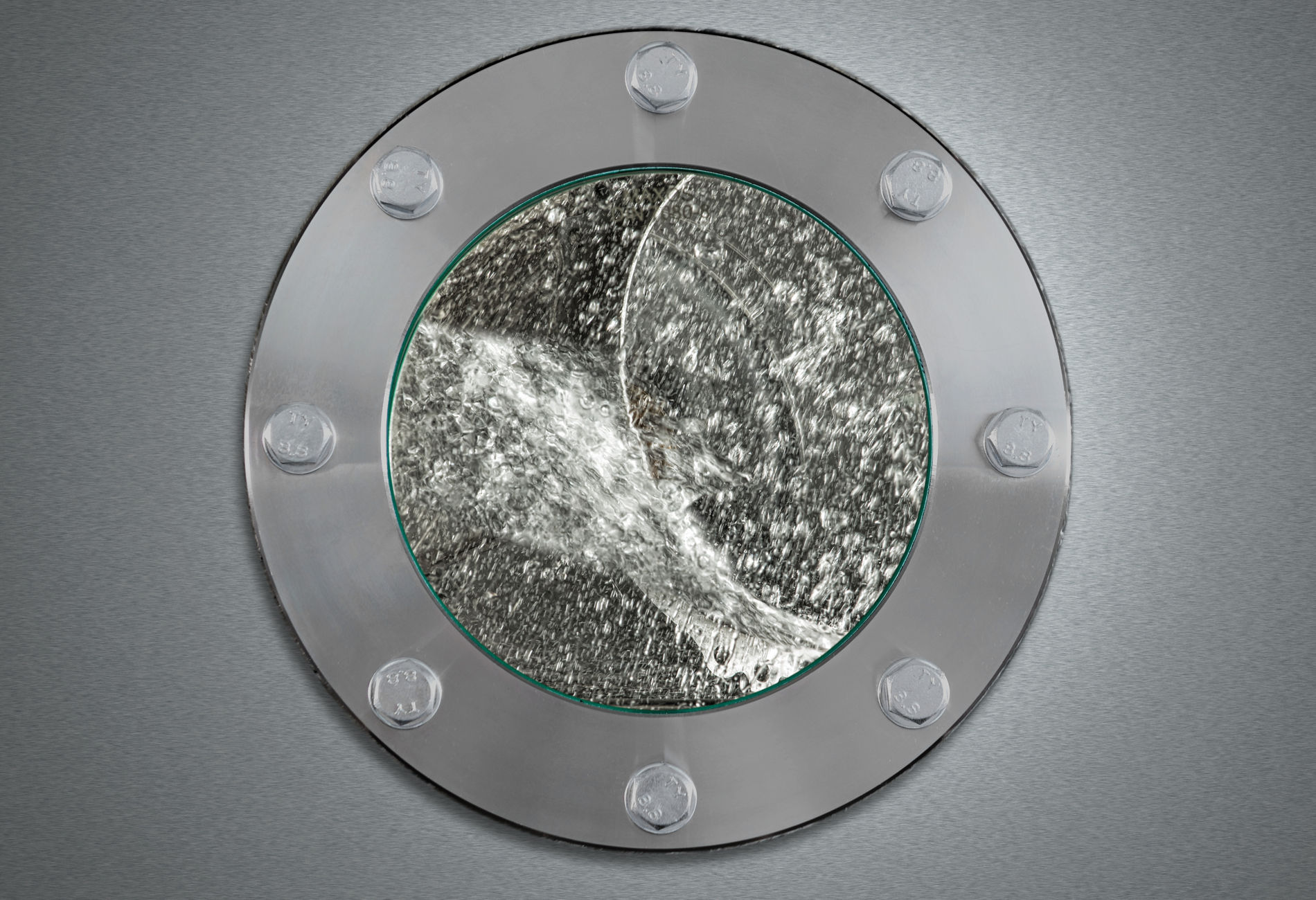
Spritzreinigungsverfahren kommen für Bauteile mit geringer Komplexität/einfacher Geometrie und mittlerem Anforderungsgrad in Bezug auf die Sauberkeit zum Einsatz.
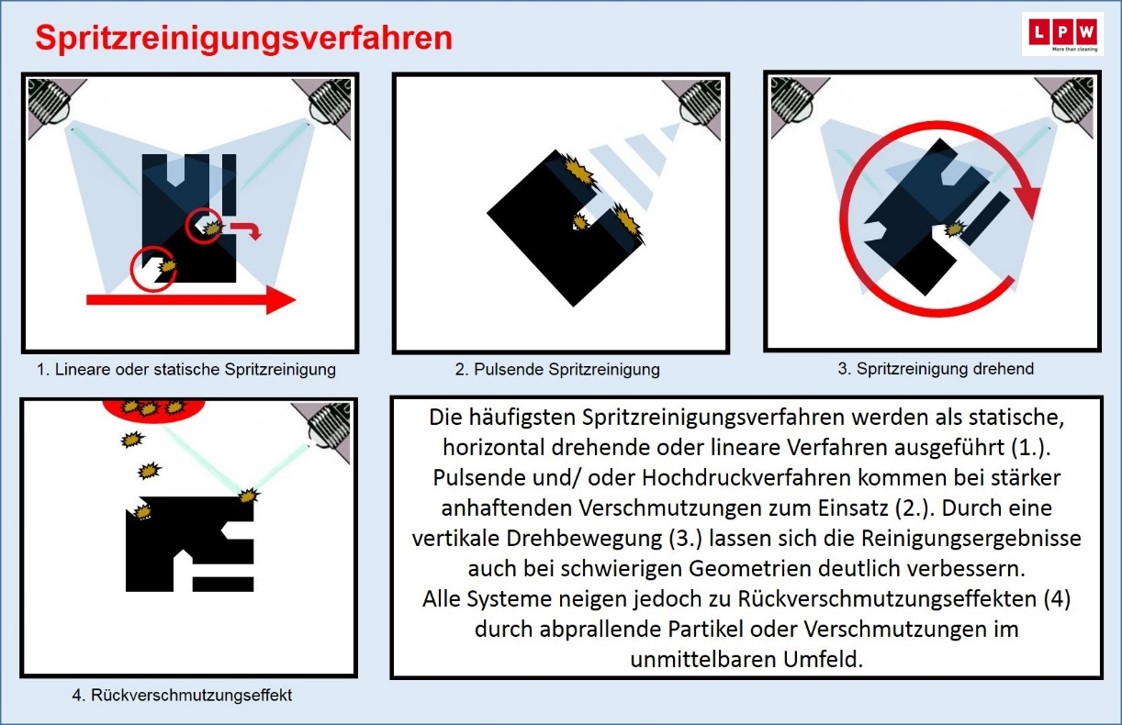
Am häufigsten werden ein- oder mehrstufige Durchlaufsysteme (LPW PowerLine) konzipiert, welche die Ware über ein geeignetes Fördersystem gleichlaufend oder taktend führen. Zur Verbesserung der Reinigungsleistung dienen Düsensysteme, die auf die Bauteilgeometrie in Ausführung, Druck und Durchflussleistung angepasst werden.
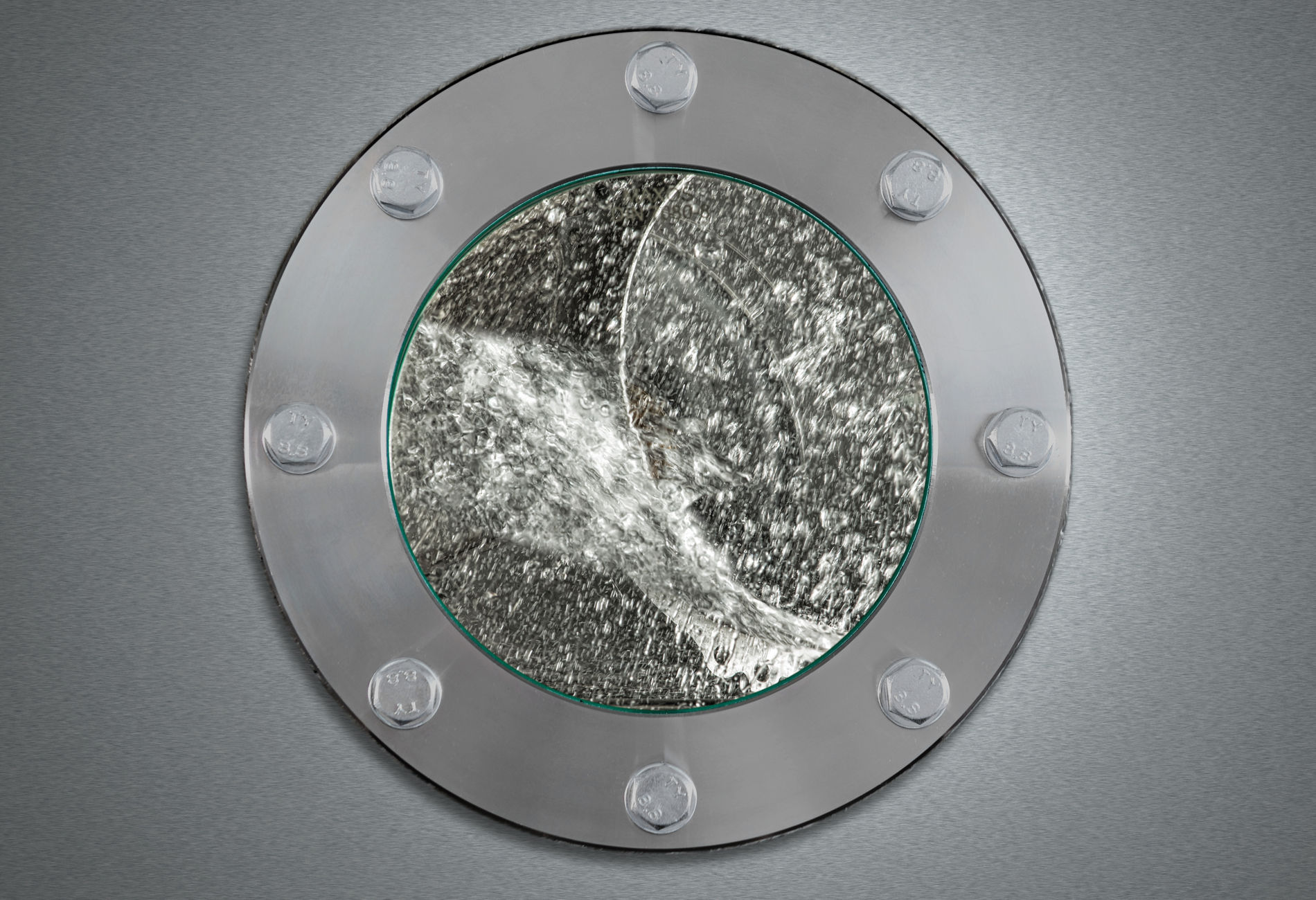
Spritzverfahren sind aber auch in geschlossenen Kammeranlagen für Korb- und Palettenware (LPW AquaJet) zu finden. Klarer Vorteil gegenüber den Durchlaufssystemen ist die bauartbedingt mögliche Relativbewegung (schwenkend oder drehend). Diese unterstützt die Reinigung erheblich und erlaubt zudem das Ausreinigen, Ausspülen und effiziente Trocknen schöpfender Partien.
Die Vor- und Nachteile der Spritzreinigung
Pro
- geringer Invest durch prozessbedingt geringeres Tankvolumen, bei Kammertechnologie geringere elektrische Anschlusswerte
- sehr gut geeignet zur Entfernung von leicht anhaftenden, auch organischen Verschmutzungen, solange die Bauteilgeometrie und die Düsenanordnung eine Komplettbeaufschlagung der Bauteiloberfläche mit dem Reinigungsmedium erlauben
- kürzere Prozesszeiten, da für Flutverfahren typische Nebenzeiten durch Befüll- und Entleervorgänge entfallen
- bei Nutzung von Durchlaufsystemen hohe bis sehr hohe Ausbringungsmengen, ggf. auch ohne Chargierung
- höhere kinetische Wirkung auf der Bauteiloberfläche, ggf. verstärkt durch pulsende Spritzverfahren
Contra
- nicht geeignet für komplexe Bauteilgeometrien
- eingeschränkte waschmechanische Möglichkeiten (Injektionsflutwaschen, Ultraschall, CNp nicht möglich)
- Gefahr der Rückverschmutzung (Abpralleffekte/Cross-Kontamination), gerade bei Durchlaufanlagen und hier bei partikulärer Reinigung
- Die Grundeigenschaften der Spritzreinigung führen dazu, dass klar definierte partikuläre Reinheitsanforderungen prozesssicher meist bis zur unteren Grenze von 500 bis 600 µm erreicht werden können. Höhere Reinheitsanforderungen setzen folgende Aspekte voraus:
- geeignete Bauteilgeometrie
- Auswahl eines geeigneten verschmutzungs- und geometrieangepassten Düsensystems (Art, Volumenstrom, kinetische Fähigkeit) im Reinigen sowie der geeigneten ganzflächigen Medienbeaufschlagung im Spülprozess
- Vermeidung von Rückverschmutzung durch hohe Volumenströme und Gewährleistung, dass die Behandlungszonen/-kammern kontinuierlich abgereinigt werden
- ausreichend dimensionierte Zonentrennungen (bei Durchlaufanlagen) zwischen den verschiedenen Behandlungsschritten