Kleinerer Zulieferer, größere Aufgaben
mo 07-08/2024
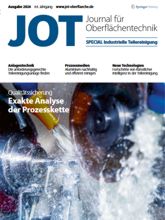
Die technische Sauberkeit im Prozess sowie die hochambitionierten Sauberkeitsspezifikationen,
vor allem im High Purity-Segment, stellen immer häufiger auch für kleinere Produzenten von
Präzisionsteilen und Baugruppen eine diffizile Aufgabe dar. Da die bisherige Maschinenausstattung
hier oftmals nicht mehr gerecht wird, ist neue Reinigungstechnik gefragt.